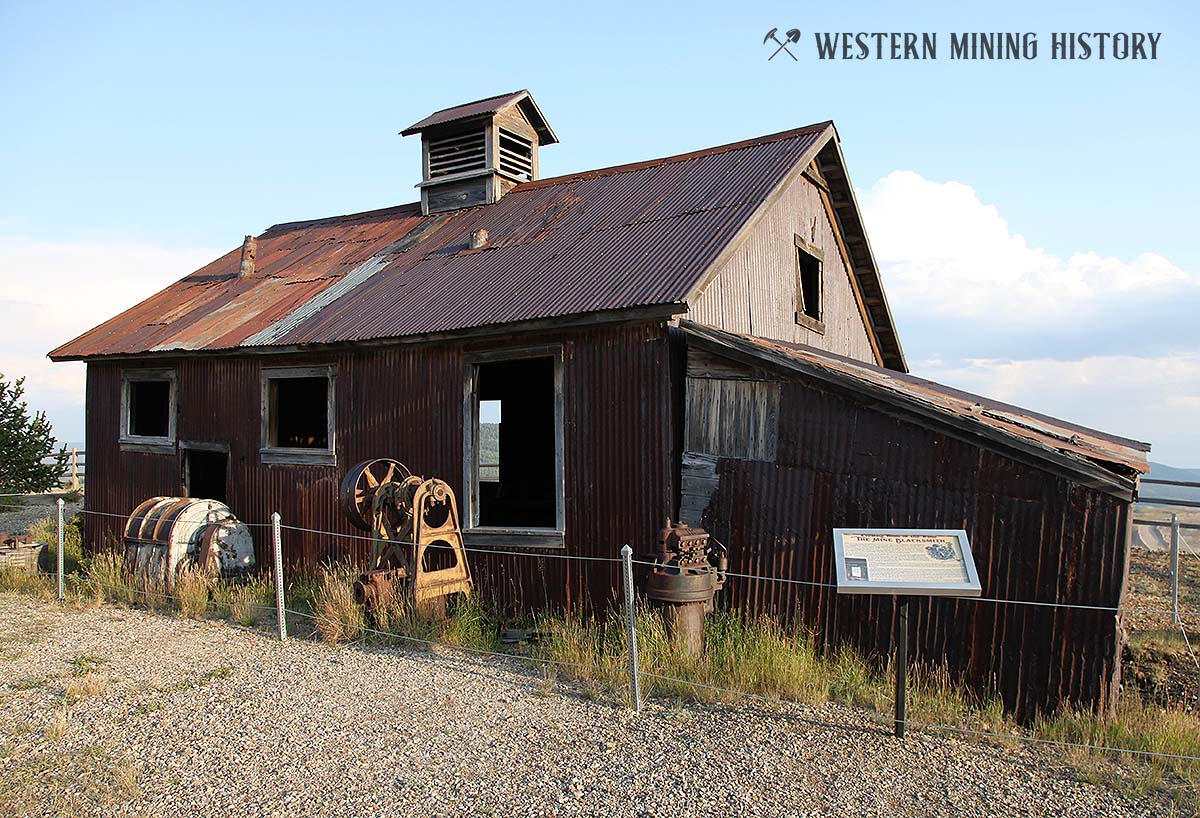
Photo Description
Creating Tools of the Trade - The Mine Blacksmith
At the turn of the century, the blacksmith shop was a vital cog in a mining operation. The remoteness of many mines forced the blacksmith to make and improvise various tools, requiring his strength, skill and design capability. Tools centered around a forge which burned coal. A large bellows was generally mounted at the forge to increase the heat of the fire. A cupola on the ridge line of the shop roof served to improve the ventilation. The blacksmith shop was required to be at least 100 feet from the ventilation intake, shaft or tunnel after several tragic mine fires were caused by sparks from the forge being sucked into the shaft when the shop was located in the same structure as the shaft or tunnel.
Before the introduction and adoption of the carbide lamp at a mine, the blacksmith made the candle spike that held a candle for the miner's illumination in the mine. The blacksmith also forged moils for cutting timber hitches and sampling, pick heads and pry bars. The major job for the blacksmith was the forging drill bits on the end of lengths of drill steel. Generally, lengths of either round, octagonal or quarter-octagonal steel were purchased from a manufacturer in lengths suitable for delivery to the mine.
In order to forge a bit for cutting into the rock, the blacksmith heated the end of the steel in the forge and as it heated, hammered it lightly on his anvil to toughen the steel until the tip of the steel turned cherry red. The red-hot steel would be hammered into a flat chisel-shaped end for hand drilling and then the steel was plunged into water to temper it.
As drill technology improved, drills run by compressed air or even electricity supplanted hand drilling. This led to better designed bits and the blacksmith used a swedge or mold of a four-point bit that he hammered into the end of the cherry-red drill steel forming the bit. Later George Leyner produced the Water Leyner, a drill that permitted water to flow through the drill machine, through the drill steel with a center hole and through the bit. The blacksmith had to be sure that the hole in the newly forged bit was kept open to allow the water to flow through the bit and help allay the dust and remove the cuttings from the drilling. The end of the drill steel that fit into the drill itself required either lugs or a collar to be formed on the side of the end of the steel or shank to help keep the steel in the machine during operation.
In 1922, the detachable drill bit was patented by a Butte, Montana, Mine Foreman, A.L. Hawksworth. The era of forged drill bits slowly came to an end as bits began to be available for purchase more cheaply than forging them. Following WWII steel bits were fitted with tungsten carbide inserts on the cutting edges giving much longer life between sharpenings. This and other improvements led to the blacksmith shop evolving into a machine shop and the blacksmith, himself, becoming obsolete.
From a sign at the site