Click on an image to get more details or a direct link.
Theresa Mine - Headframe and Ore Bin
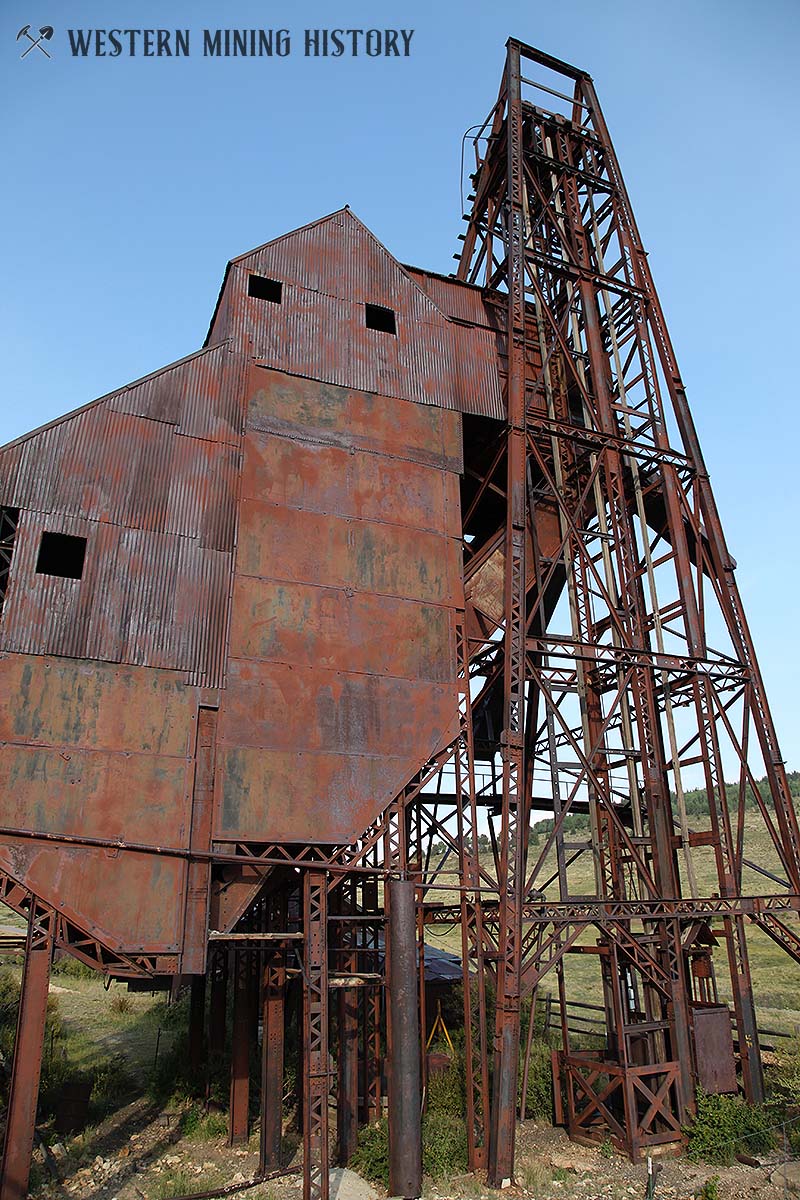
Mine History
A number of mining companies owned and operated this mine from 1895 to 1961 including the Theresa Gold Mining Company, the Vidicator Consolidated Gold Mining Company, United Gold Mines Company and Golden Cycle Mining Company. The property was operated through the years alternating with years of idleness.
Production
Records indicate that the mine produced over $2,500,000 in gold or over 120,000 troy ounces, when gold sold for 20.67 per ounce.
Surface Plant
The three-compartment Theresa shaft was developed to a depth of 1,620 feet and was serviced by a Wellman, Seaver, Morgan double-drum steam hoist. Power was supplied by at least one 250 Hp Babcock & Wilson water tube boiler. The four-post derrick-type timber headframe stood over the shaft. Rock was transported through the shaft in mine cars on two small, double-deck cages.
The entire surface plant was destroyed by fire in 1934. The headframe was replaced with the present steel structure and the plant was upgraded with a metal hoist house, a metal ore house incorporated into the headframe structure and a new change room.
Additional exploration, carried out in 1961, failed to give promising results and coupled with the closing of the Carlton Mill led to the final closure of the Theresa Mine.
Powder Magazine
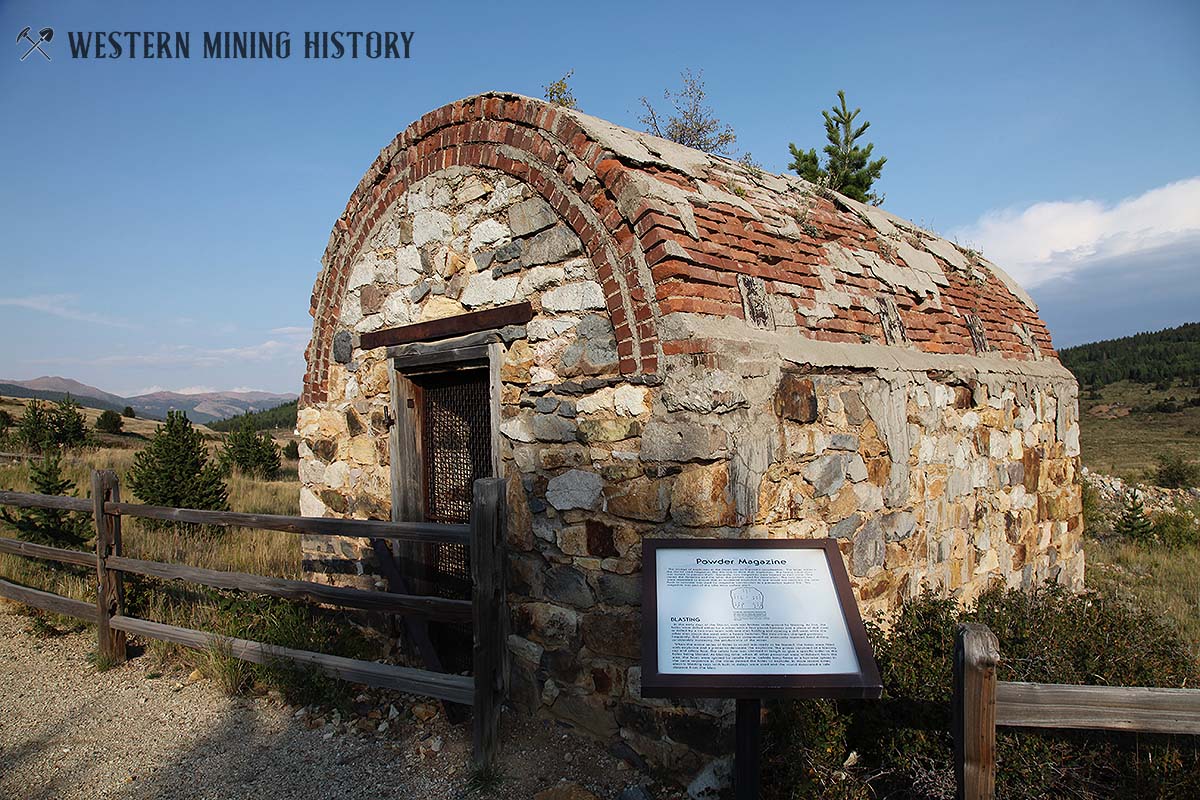
The storage of explosives at the mines was an important consideration. The larger mines in the district used magazines built of brick in which to store explosives. The heavy metal door was locked to prevent theft. Generally, two magazines were located at each mine. One was storage for the dynamite and the other was for the primers used for detonation. The two structures were separated to ensure that an accidental explosion in one would not detonate the other. Rock or concrete was used for magazine construction as a precaution against fire. This magazine belonged to the Golden Cycle Mine and was also used by the Anna J. Mine crews.
In the early days of the District, rock was broken underground by blasting. At first, the holes were drilled either by a miner with a four-pound hammer and a piece of drill steel or drilled by a two-man team with one man holding and rotating the drillsteel while the other man struck the steel with a heavy hammer. The two miners changed positions frequently. Drill machines, powered by compressed air eventually replaced hand drilling, considerably increasing the productivity of the miner.
From a sign at the site
Vindicator Valley Trail - Goldfield Seen in the Distance
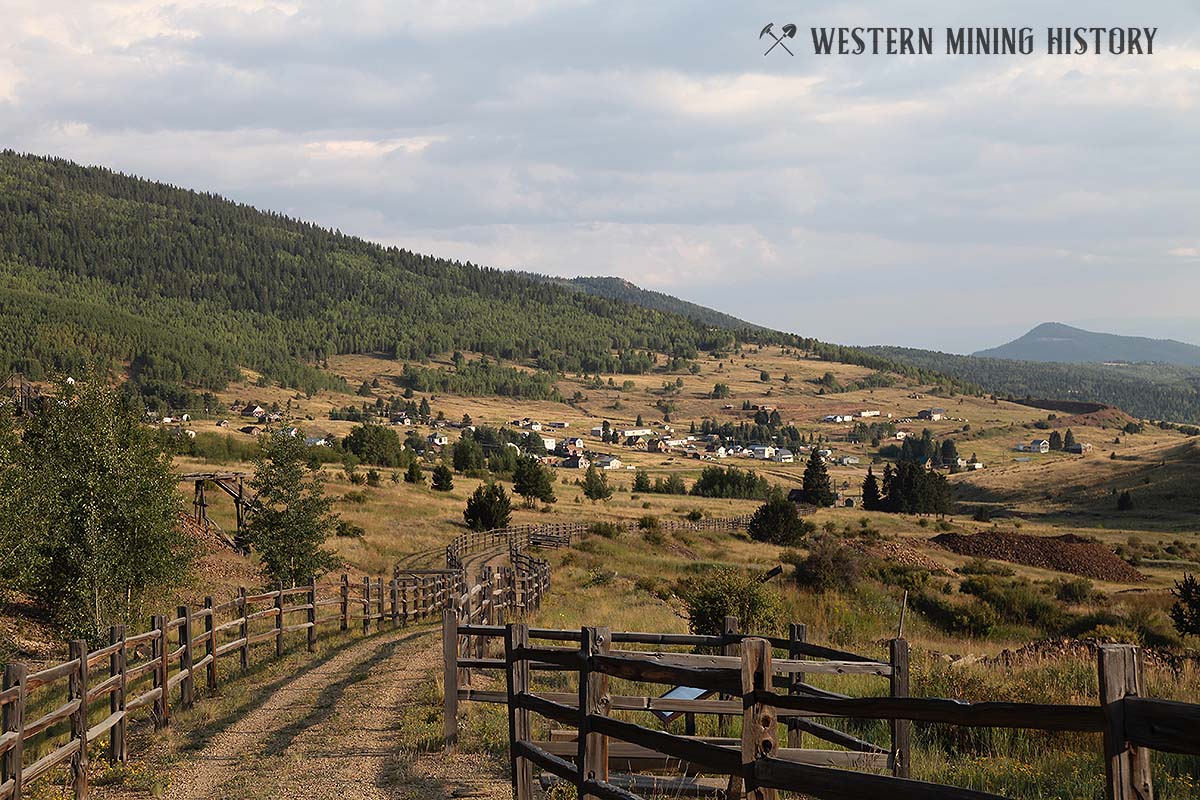
On the Vindicator Valley Trail - a two mile trail outside of Victor.
American Eagle Mine
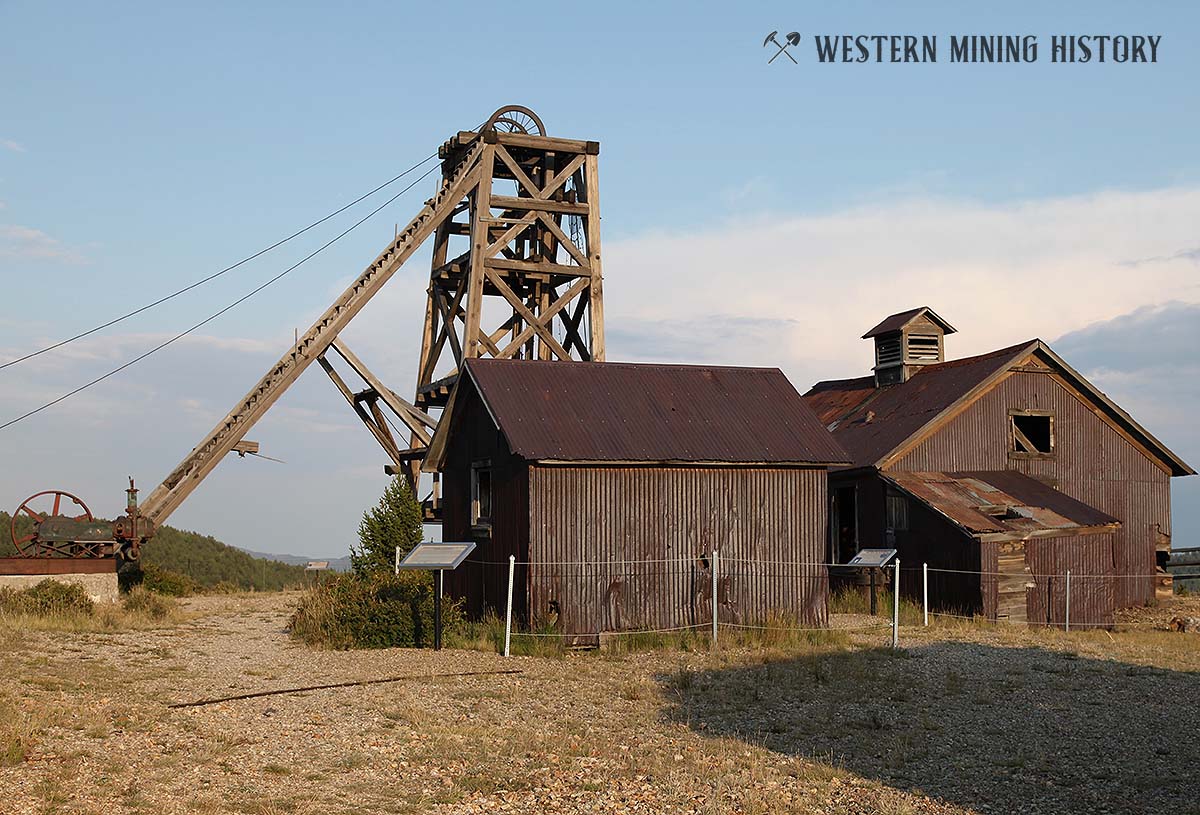
On this bluff in the late 1800's the highest underground mine in the Cripple Creek Mining District was collared in at an elevation of about 10,750 feet above sea level. In 1895 William S. Stratton purchased the operations and worked them under the Stratton Cripple Creek Mining and Development Company. Also at this site is the remnant of the blacksmiths forge building used at this mine.
The American Eagles Mine involved three shafts and the workings were further connected to adjoining properties. The underground workings reached 1,540 feet below you by 1902, making it the deepest shaft in its time. The workings progressed deeper, but production and shipping of ore was sporadic until 1936 when a rich strike was made between the 19th and 21st levels (1900 and 2100 feet below you). The mine produced ore worth at that time $7 per pound.
Headframes sit above the vertical shaft in order to support the sheave wheel or pulley system that passed the hoist cable from the steam- or electric- powered hoisting mechanism to the metal cage that hauled workers and equipment down into the workings and ore and workers out to the mine. At this site a Stearns Rogers Company double-drum hoist, still in place north of the headframe, did the job. The 750 hp hoist was powered by steam, which was generated in coal-fired boilers using water supplied by the Altman Water Company. Workers were lowered into the the workings and brought up at shift changes. Ore would be raised and supplies lowered between the shift changes. The Mollie Kathleen Gold Mine Tour near Cripple Creek offers a chance to experience this unique trip to work. Double-drum hoists allowed the use of two cages, or platforms, one rising and one lowering simultaneously. Examples of other hoists, cables and flat ropes may be viewed at the Victor Lowell Thomas Museum as well as the Independence Mine and Millsite Trailheads.
The wooden headframe, while generally characteristic of headframes in the District, provided an example of a more unique feature - that of detaching hooks. These hooks were designed to release the main cage should the hoistman overwind the hoist cable so that the man cage would rise up toward the sheave causing injury to miners.
From a sign at the site
American Eagle Mine Blacksmith Shop
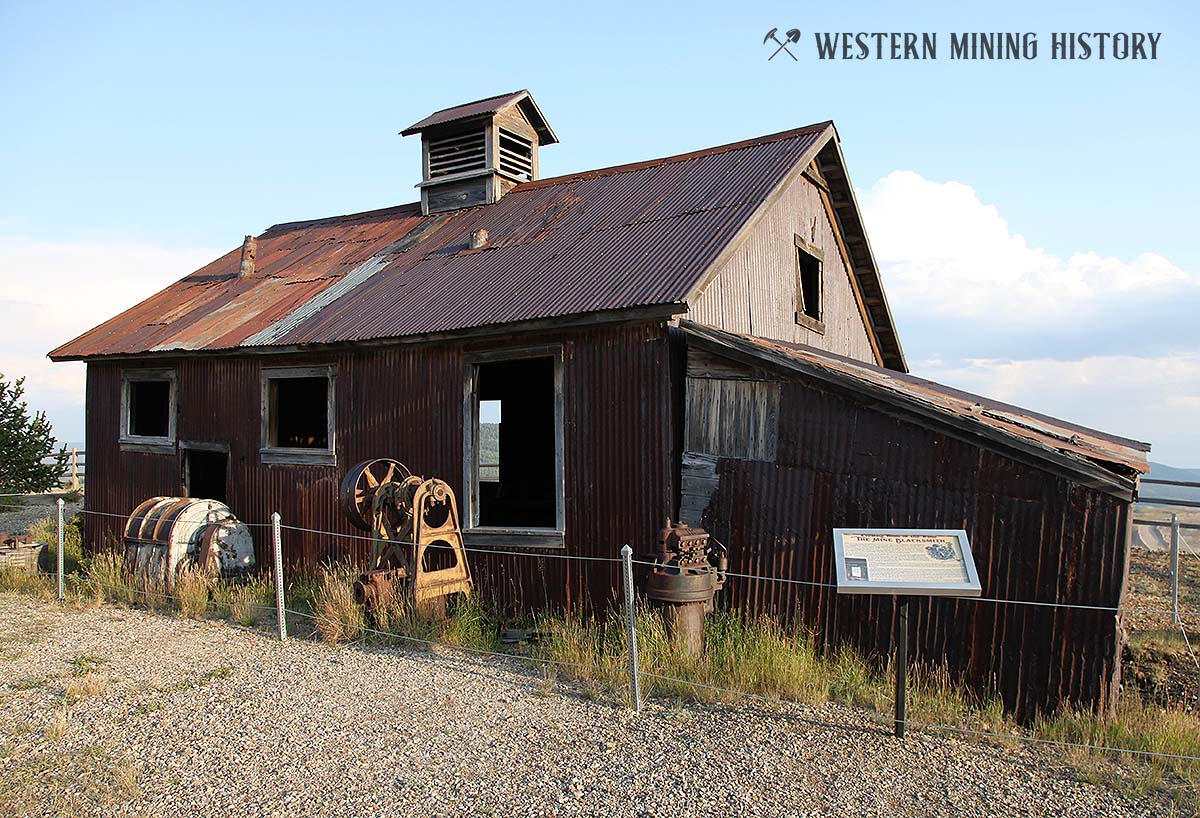
Creating Tools of the Trade - The Mine Blacksmith
At the turn of the century, the blacksmith shop was a vital cog in a mining operation. The remoteness of many mines forced the blacksmith to make and improvise various tools, requiring his strength, skill and design capability. Tools centered around a forge which burned coal. A large bellows was generally mounted at the forge to increase the heat of the fire. A cupola on the ridge line of the shop roof served to improve the ventilation. The blacksmith shop was required to be at least 100 feet from the ventilation intake, shaft or tunnel after several tragic mine fires were caused by sparks from the forge being sucked into the shaft when the shop was located in the same structure as the shaft or tunnel.
Before the introduction and adoption of the carbide lamp at a mine, the blacksmith made the candle spike that held a candle for the miner's illumination in the mine. The blacksmith also forged moils for cutting timber hitches and sampling, pick heads and pry bars. The major job for the blacksmith was the forging drill bits on the end of lengths of drill steel. Generally, lengths of either round, octagonal or quarter-octagonal steel were purchased from a manufacturer in lengths suitable for delivery to the mine.
In order to forge a bit for cutting into the rock, the blacksmith heated the end of the steel in the forge and as it heated, hammered it lightly on his anvil to toughen the steel until the tip of the steel turned cherry red. The red-hot steel would be hammered into a flat chisel-shaped end for hand drilling and then the steel was plunged into water to temper it.
As drill technology improved, drills run by compressed air or even electricity supplanted hand drilling. This led to better designed bits and the blacksmith used a swedge or mold of a four-point bit that he hammered into the end of the cherry-red drill steel forming the bit. Later George Leyner produced the Water Leyner, a drill that permitted water to flow through the drill machine, through the drill steel with a center hole and through the bit. The blacksmith had to be sure that the hole in the newly forged bit was kept open to allow the water to flow through the bit and help allay the dust and remove the cuttings from the drilling. The end of the drill steel that fit into the drill itself required either lugs or a collar to be formed on the side of the end of the steel or shank to help keep the steel in the machine during operation.
In 1922, the detachable drill bit was patented by a Butte, Montana, Mine Foreman, A.L. Hawksworth. The era of forged drill bits slowly came to an end as bits began to be available for purchase more cheaply than forging them. Following WWII steel bits were fitted with tungsten carbide inserts on the cutting edges giving much longer life between sharpenings. This and other improvements led to the blacksmith shop evolving into a machine shop and the blacksmith, himself, becoming obsolete.
From a sign at the site